(
Satellite, the "North Mill" contained the blast furnaces and BOF)
The plant stretched for miles along the east bank of the Ohio River. ("The Jones & Laughlin Steel Works gobbled up mile after mile of shoreline, producing beams, billets, bars, cans, wire, sheets, rolled steel—nearly every imaginable finished product" [
PaulHertneky])
This plant provided cast and rolled rounds to the
Campbell Plant to make seamless pipe.
 |
LC-USZ62-119059 Steel plant on the Ohio River. Aliquippa, Pennsylvania SummaryBird's-eye view of Jones & Laughlin Steel Company plant rooftops and rail yard.Contributor NamesRothstein, Arthur, 1915-1985, photographer |
.jpg) |
Jessica Van Giana posted 5 Blast furnaces. Aliquippa Works Mostarifa Mostarifa shared |
The following photo allowed me to determine the satellite location of the North Mill.
 |
silogic, this page has a lot of postcards. It used to have five blast furnaces. An aerial view of the North Mill, Aliquippa Works, showing blast furnaces (center) and BOF (upper left), ca 1970. (Courtesy of Charles Fluharty from the book Portraits of Steel) P&LE tracks at the left. PRR tracks on the on the other side of the Ohio. Gordon Zernich posted Aliquippa North Mills Works way back when/the new BOF is to the upper left.
Patrick Martin: The flagship of J&L. Mark Henry: What does BOF stand for? Blast open hearth furnace? |
 |
David Holoweiko posted Blast furnace #4 1933 J&L Aliquippa PA |
 |
Jessica Van Giana posted 5 Blast furnaces. Aliquippa Works |
 |
Graham Whitefield commented on Mark's question
Basic Oxygen Furnace. Charged with molten iron, steel scrap and additives to obtain the required final grade. |
Cory M. Roma
posted two images with the comment: "These are probably my two favorite photos of the old J&L Steel Aliquippa Works from my hometown! My grandfather worked here for over 25 years, from the moment he graduated high school in 1957 to when LTV shut most of the plant down in 1984."
 |
1 |
 |
2 |
 |
Gordon Zernich posted the marker was located on the lot of the train station which was located near the main tunnel entrance. From my reading here it would seem that the Gary USS works must have started operation after 1909 |
 |
TimesOnline, Beaver County Times The north mills of J&L. |
 |
Phil Jad posted
J&L Steel Aliquippa Works Around 1985 |
 |
Phil Jad posted
J&L Steel Aliquippa Works Blast furnace being demolished Dwayne Lester: We taught them…..then they made it better….and now we buy from them…. James Ujevich: Dwayne Lester we never changed with the times as long as a profit was being made. Imports started rolling in in the late 70s and the collapse came in 82. No chance of a job for us out of high school then. |
 |
Karen Simpson posted North mills..West Aliquippa, Pa. |
 |
bcpahistory "In the 1960s there were 14,970 Steelworkers employed in Aliquippa alone. In 1997 there were slightly less than that number employed in Allegheny, Beaver, Butler, Fayette, Washington and Westmoreland counties combined." |
 |
Jackson-Township historical preservation posted
View of the J & L (Jones & Laughlin) North Steel Mills the day after they turned off the lights in Aliquippa, Beaver County in 1985. |
 |
Little Beaver Historical Society posted Mesta 4 High Temper Mill at the Aliquippa Works of J&L Steel 1-14-1936. |
 |
David Holoweiko posted Assorting floor J&L Steel Aliquippa Tin Mill 1915 . Look how many women working in 1915. Carol DeVincent: It's where my mother worked. She had the tip of her nose cut off from sorting. Robert Scott Davis: They’re inspecting sheets of tin. [Sorting tin must be tedious work, and thus considered "women's work," because I've seen other photos of women sorting tin when we were not at war. In fact, some of the comments confirmed this observation.]
Scott Gracie: For a very long time, women in the steel industry were relegated to tin floppers in the tin mills, doing quick inspections and sorting. The exceptions to this were during the wars, specifically in WWII. When the war was over, the women were displaced by the returning GIs to steelmaking. I had two aunts, then in their very late teens/early 20s, that operated overhead cranes at Weirton Steel during the war. In the mid '70s after the EOE, women would return to all hourly positions in the mills. Karen Simpson: Scott Gracie ...yup. I was hired in 1975. Worked for coal Handling in the Byproducts in West Aliquippa. Ran coal on conveyor belts to the coke ovens. Than my last year or so I bid and worked in the Lab until the mills started closing. I was terminated in 1984. Sad. Had hoped of retiring from there. Chris Dawson: Yes, the US didn’t enter the war until 1917, but steelmakers and other companies were doing good business supplying materials to the Allies after the war broke out. But the women in the picture weren’t likely replacing men; tin mills long had women employees, who would be used as inspectors of the tinplate, because women were viewed as more likely to spot any imperfections in the shiny tin than men could. So that’s why “tin floppers” (so called because they would quickly inspect one side and “flop” it over to inspect the other side) were almost always women. |
 |
David Holoweiko posted J&L Aliquippa PA 1950 Real Bubba: South mills, at 10 miles long Aliquippa works can’t fit in one picture.
Scott Gracie: Based on what I've read, LTV closed Aliquippa down in '84.......I don't know, if it was progressive (hot end first, then tinplate later ?). According to research, the hot end did close in '84.....the Tin Mill operated under USS and closed in 2000. Steel will be coming back to Aliquippa in the near future under 72 Steel. |
Cory M. Roma
posted five photos with the comment: "Since my last post of the J&L Aliquippa Works sparked a lot of interest, I’ll share a few more photos to round out the evening!"
Jim Wood: Can see my old mill in the pics, Armco, across the river from JL. Thanks
Tim Grau: Great pics. It was a massive plant. 7 miles long?
Cory M. Roma: Tim Grau Yes sir!! I think it employed 14,000 at its peak. It was J&L Steel’s flagship mill until the day it shut down, and its first fully integrated steel mill.
 |
1 |
 |
2 |
 |
3 |
 |
4 |
 |
5 |
 |
π
π΄πΌπ΄πΌπ±π΄π
π
π·π΄π½: πΏπ΄π½π½π
π
π»π
π°π½πΈπ° posted
Jones and Laughlin Seamless Tube Mill Loc: Aliquippa |
 |
George A. Koval posted J&L Aliquippa Works, North Mill, 1964 Paul Cashdollar: 7 miles of mill! 15 million cubic feet of oxygen per day! Mostly all gone! |
 |
Bill Fair commented on Roz's post A post card, I believe. All gone.
|
 |
David Holoweiko posted
Very interesting photo showing J&L Aliquippa PA, building blast furnaces 1 2 and 3 in 1909 . Interestingly if you look to the left center the sign for the entrance to Aliquippa amusement park has not yet been taken down. The mill was built on the site in the park and many park buildings were reused for the steel mill. Photo courtesy Wayne Cole's book Ghost Rails X Iron Phantoms |
 |
History US Moments posted January 1941. Jones and Laughlin Steel Company. Beehive coke ovens. Aliquippa, Pennsylvania. Photo by John Vachon.... James Torgeson shared |
 |
David Holoweiko posted South Mill Welded Tube J&L Aliquippa , PA works 1935. |
 |
Phil Jadlowiec posted Pittsburgh and Lake Erie with J&L Aliquippa works in the background. Michael B Huwar: J&L BOF North Mills |
 |
Phil Jadlowiec posted
J&L Steel Aliquippa Works James LaParr: Those rail cars might have had Benson Mines product in them. [According to some more comments, J&L owned the mine and it was at Star Lake, St Lawrence county, NY. |
 |
Raymond Boothe posted Painting of the blast furnaces of the Jones and Laughlin blast furnaces at Aliquippa, Pennsylvania (Dr. Raymond Boothe collection). |
 |
Bob Ciminel posted J&L Wire Mill Russell Weidner: Bob Ciminel Aliquippa was the only location for J&L rod and wire products. Pat McCon: Aliquippa. South Coke Works - see the beehive coke ovens [which is a very old technology] and the South Power House. As I recall, the buildings on the left are probably the rod mill - the wire mill was the next operation to the South. The #20 Hose House (South Mills Fire Station) was on the road between the Tin Mill and the Wire Mill. The South Mills Restaurant was also in that area, as well as the South Dispensary - but those were before my time. On the right at the top of the photo is, I think, the south end of the Tin Mill. Trivia: At Aliquippa we gave directions as ‘north, south, hill, and river’. Even the crane controls were labeled that way. In this photo the river is to the right. The photo was taken nearly directly above the Ambridge Bridge. J&L Aliquippa Works South Mills - about 25% or so of the South Mills. Frank Seidita: Pat McCon I was working for a guy in Kentucky he was a blast furnace man he always use the signals up river down river hillside and Riverside. I always believing in north south east and west, ask him where he got that from? He said the drawing. I didn’t believe him and he took me down to his trailer and showed me on the drawing he was right! |
 |
David Holoweiko posted
Aerial photo showing the ten inch Skelp mill white roof . The 14 inch rolling mill t-shaped building . J&L Aliquippa PA The mill across the Ohio River in Ambridge is the A.M. Byers company . |
 |
David Holoweiko posted Number one blast furnace J&L Aliquippa PA Beaver County PA |
 |
David Holoweiko posted
An old photo of the South Mill Power House J&L Steel Aliquippa PA in the mid winter. Note the old Bee Hive Coke Ovens in the for-ground. From my late friend Don Inman's Beaver County Industrial Museum archive. |
 |
David Holoweiko posted Charging Machine over a coke battery J&L Steel Aliquippa PA 1980. Ken Jamin: The car charged the ovens. What did the guy with the long pole do? Scott Andrejchak: Ken Jamin the was a hook at the end of the stick to pull the lids off, so the Larry car could put coal into the battery. Those white manhole covers are the lids. And each battery takes a different type of coal, depending on the type of coke they making. Which is why if you look, the lids line up to where the crushed coal is going to come out. Ken Jamin: Scott Andrejchak And who closed and sealed them behind the Larry car? Scott Andrejchak: Ken Jamin the same guy that takes them off, as I recall. It was a summer job at Hazelwood plant. We had wooden shoes that went over the shoes/boots you wore. |
 |
Gregory Wolf posted Jones and Laughlin steel mill in Aliquippa, in Beaver County, Pennsylvania, located about 30 NW of Pittsburgh on the Ohio River. January 1941. Bill Sutliff: Ross Patterson -there is a very good chance that sign was made in Beaver Falls at the Ingram-Richardson porcelain enamel sign plant. Jeff Sherrill: Bill Sutliff. It was made there...!!! Largest porcelain sign in the world for years... |
 |
Stever Hoschar Sr. posted My father in law worked there. Ronald Cumberland: Thank you for sharing this was J L biggest mill at 1 time think there was 5 blast furnace at one time the tin mill was the last thing running. |
 |
Eric Krithinithis posted Raymond Flynn: We use to store some Iron Ore and Pellets in Lorain,Ohio and ship it there during the 60's! Phillip King: I worked there as a contractor in the early 80s, when they rebuilt the old recycled Sheet & Tube round mill, Millions of dollars spent on overtime to put it together, I don't think it ran 6 months before they shut it all down and started demolishing the whole mill. Very sad time in the Beaver Valley. Jason Sessoms: Rade Vukmir wrote an excellent book called the mill which was about the aliquippa works. |
 |
David Michael Moslen posted [I depromoted this to a small size because Eric's photo is better.] J&L Aliquippa Works...my Father worked there...32 years... Pat McCon: Can’t remember if things were numbered north to south or vice-versa. Is that A1 or A5 cast house? I think A5, but not sure. Samuel Peoples: That is the A-5 cast house. The furnaces were numbered north to south. The building on the right is the boiler shop where the sub ladles were rebuilt. The tall building on the right is the north mill powerhouse and blow engine room. Bill Franz: Totally integrated steel mill. Coke plant, furnaces, caster and sheet, roll, welded tube and seamless tube. 7 miles long and 21/2 miles wide. |
This photo was a part of a video about the
new Shell plant. It implies this was on the location of their new plant and it called it a smelting plant. Instead, I think this was the remaining blast furnaces of the J&L Wire Mill.
Keenan Quinn Shaffer
posted two photos with the comment:
J&L Steel Aliquippa Works (later LTV Steel) years before it was razed, and the fake left arms my old man used in the mill.
He was a maintenance welder, and taught the USW Local 1211 apprenticeship for a few years. Lost his left arm, partial knee on the same side and suffered severe shrapnel damage as an Army sergeant in the initial invasion into Korea from Japan in 1950 to start the Korean War. Died in 1989 from work-related cancer at 59.
My uncle on my dad's side was killed on the job in the mill, in 1972.
J&L Aliquippa was roughly 7 miles long between Aliquippa and Monaca, PA along the Ohio River, roughly 15 minutes north of Pittsburgh. I still have some pipe made in J&L. Nothing made today is touching it...the best.
 |
1 |
 |
2 |
 |
David Holoweiko posted Number 5 blast Furnace coming down J&L Aliquippa. Allan Beighley: A-5 Blast Furnace was the first furnace that I broke-in on in 1970 when I finished the Production Management Training Program. I was a Casthouse Blower Foreman in the department until the end of 1974 when I moved up to General Headquarters - Pittsburgh in the Purchasing Department. I fondly remember the old steam gun on A-5, tapping the "monkey", and helping change burned tuyeres during shutdowns. During my tenure in the furnace department, I blew on A-1, A-3, A-4, and A-5 furnaces, was a Linerunner, Pig Machine General Foreman, and general backup on special projects to Al Herbenak the department Engineer. Howard Maher: You wouldn’t happen to know when the BOFs went away, would you? We watched them being built from across the river in Baden, with an oxygen pipeline coming over the Aliquippa hills supposedly from West Virginia… Pat McCon: Howard Maher - #1 BOF was closed when #2 was built - late 60s. #2 was shut down around 1985, demolished soon after. Some time in the 70s the oxygen line ruptured - where it crossed under Raccoon Creek, I believe. Big boom. The valves were far apart - it took a long time for the line to drain so the fire could be extinguished. |
 |
David Holoweiko posted Charging BOF1 April 1960 at J& L Aliquippa Works. James Robert Dinsmore: Was this a different BOF than the one on what was formerly Crow Island? Pat McCon: James Robert Dinsmore - Yes #1 BOF and the BOF at Cleveland Works were built about the same time, about 1959. When they were successful, #2 BOF was built on the backfilled Crow Island, ca. 1968. |
 |
David Holoweiko posted Bessemer Converter J&L Aliquippa works . Last used in 1968.
Michael Sweeney: Bessemer was a pioneering steelmaker. Problem was high phosphorous in the melt. Ok in the days of riveted steel but not for welds. Open hearth then bof took over Surprised to see one running as late as 1968. |
 |
David Holoweiko posted Another blooming mill 45" blooming mill J&L Aliquippa works. Joel Sundholm: At a time, when there was little faith in continuous, casting! Bernie Fedak: Joel Sundholm AMEN! I quote a LTV executive "continuous casting will never work" John Boucek: A great decision!?! Brian Olson: John Boucek Another example of bone headed Thomas C Graham leadership decisions that drove J&L in bankruptcy. That blooming mill should never have been built. They wanted more blooming capacity to supply seamless tube which turned on them. Robert Witherow: What a mistake that was….another LTV blunder as usual. Bernie Fedak: Very short lived! [Continuous casting made ingot teaming, stripping, soaking pits and blooming mills obsolete.] |
 |
Bob Ciminel posted In 1953 a major expansion project to increase steel production at Jones & Laughlin Steel Corporation’s Aliquippa Works was undertaken. A new 44-inch blooming mill and its drive were installed, replacing a steam-engine drive mill that set many production records during its time. The installation process was accomplished in the remarkable time of 7 days and 14 1/2 hours of down-time. The 44-inch Blooming Mill was driven by four 3000-hp, 70 to 140-rpm, 750-volt, double-armature motors, arranged in tandem twin drive. The main drive motors drew their power from a motor-generator set (pictured here) consisting of four 3000 kilowatt, 750-volt, d-c generators, a 15-foot 10-inch diameter, 220,000 pound steel plate flywheel (left foreground), and a 9000-hp, 6600-volt, 360-rpm induction motor. The 44-inch Blooming Mill was shut down in October 1984. |
 |
Comments on Bob's post |
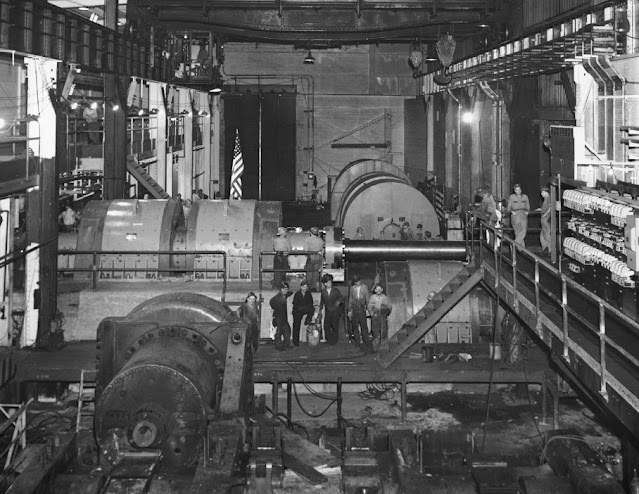 |
Bob Ciminel posted Motor replacement at J&L Aliquippa Works in 1953. Pat McCon: Donald R. Inman - Was this the Blooming Mill conversion from steam to electricity? Rick Rowlands: Pat McCon Yes Rick Rowlands: This is when the blooming mill engine (foreground) was replaced with electric motors and shows the motors in service before the remainder of the engine had been removed. Alan Taylor: The motors look like the 2500 HP General Electric motors we had in the 4 stand at USS Stelco. In the back that looks like a motor generator set. Richard Peoples: So it was told to me, the mill gearbox and mill housing was set out on the riverbank for scrap but then sold down the river to Wheeling-Pittsburgh Steel and installed at Mingo Junction with electric motor. In 1980-82 I was the QC metallurgist for it in Mingo. It was a great-performing 44" high-lift mill. Donald R. Inman: Yes it was. All the work was done in 7 days, from shutdown to start up. Even removing the steam engine put in 1909. Sam Burkett: didn't they have a steam operated blooming mill? Rick Rowlands: Sam Burkett Yes and the remaining part of the engine bed plate is in the foreground. Sam Burkett: when i was there around 1979 installing the seamless tube mill, I could hear it running. |
 |
Jack Snodgrass commented on Bob's post Rewinding one of a ball mill motor back in the 80's... |
 |
Bob Ciminel posted [or was this done in Pittsburgh?] Setting an extension shaft, J&L Steel, 1953 Chuck Pilant: Looks like our drive spindles on our roughing mill but ours were larger diameter and longer. Took alot of finesse, and patience to change them out. |
 |
Bob Ciminel posted Setting motor brushes, J&L Steel, 1953 [or was this done in Pittsburgh?] [I think it is interesting how the "wires" are in fact rather wide bars.] Fred Lannert: Our horizontal mill had two 7000hp motors. Each motor had 394 brushes. Commutator was 7’ in diameter. It was a good job in the summer because there were only a few places that had air conditioning, and that was one of them. Ronald Hollingsworth: Yes I remember doing brushes on motors like these, the bottom two rows are always the hardest laying upside down on your back. Rose BZ: Always helps when guy in a suit stands over you whistling. John Sims: Yes! I did weekly brush maintenance on our mill motors and M-G sets. It wasn't too bad as long as I stayed on top of (and under) them. Bob Ciminel: Changing out carbon brushes was a dirty job. You looked like a coal miner when finished. Ron Lattanzio: If I had a nickel for every brush I changed, and every comm I stoned, I'd be rich! |
 |
Bob Ciminel posted J&L Steel, 1953 [I'm guessing that this was in Aliquippa instead of Pittsburgh.] Larry Oatman: Small motors. National Steel blooming mill motor was 10,000 horsepower. |
 |
Bob Ciminel posted J&L open-hearth ladle pouring ingots. J&L's railroad, the Aliquippa & Southern has a hopper spotted behind the ladle. Date unknown. |
 |
Bob Ciminel posted J&L pickling vats, date and location unknown but probably not the Heinz plant. Pat McCon: Might be the Welded Tube Department at the Aliquippa Works. They had vats like that. Mike Seeger: Pickling has to be the most vile process in all of steelmaking. [There are several comments about the acid fumes destroying the worker's teeth. It evidently removes the tooth enamel, turns the teeth black and then causes them to be removed.] Robert Cody: I swear you could literally watch people die. But the bonus was so good there was never a personnel shortage. They most all were toothless |
 |
Bob Ciminel posted J&L Steel The descriptions says "Tapping Machine," but those look more like milling machines to me. Any expert opinions would be appreciated. Pat McCon: Look on the floor - couplings. I suspect it’s the Coupling Shop at the Aliquippa Seamless, where the couplings were made for the Tube Mills. If it’s a J&L photo it has to be Aliquippa because that’s the only place we had tube mills before they bought YS&T. [Several comments indicated that this machine would tap big threads.] |
 |
Don Cassata posted Brian Olson: J&L Aliquippa 44" hot mill
|
 |
David Holoweiko posted 44' Hot Strip Mill J&L Steel Aliquippa. Built 1957 and was the first computer controled mill in the world. The Westinghouse Prodac computer running the reversing mill was solid state and measured about five feet hight, five feet wide and about two feet deep. Programed by a card reader that was about four feet high, high five feet wide and about three feet deep. It did work well and was still in operation when the mill shut down in 1982.
Allen Weber: Westinghouse Prodac was also used at US Steel's South Works where it controlled our 53" Blooming Mill. |
 |
David Holoweiko posted The first ingot being rolled in the new 44-inch blooming mill built during Jones & Laughlin Steel Corporation’s Aliquippa expansion project in 1953. Al Monroe: is that a huge fan they are behind on the left? Dennis Ferguson: Al Monroe It blew the steam away!
Jerry Eiseman: Watched inside pulpit rolling I beams thru Thick glass scared by flying metal if operator rolled to fast beam would curl up to window and he would stop and reverse Pat McCon: Great photo. But poor place to stand. The operators were behind bullet-proof glass; these guys were standing right in the line of fire. π΅π« Graham Whitfield: Pat McCon Agree with you Pat, a very hazardous place to spectate. At our Slabbing Mill in the 1960’s they would have been showered with hot scale after the first pass. Larry Keating: Changed a lot of blooming mill rolls. One time changed rolls twice in same day never made one pass. The top or bottom roll had broken in half. Kevin Tomasic: There's still a bloomer at USAP in Bridgeville. Handles mostly alloy ingot, rolling these into slabs or bars. |
 |
Bob Ciminel posted J&L Steel, 1942 Samuel Peoples: That picture is from the 14" Mill at Aliquippa Works. The saw is one of two, on the output of the cooling beds. worked there in 1963-64 |
 |
Bob Ciminel posted Flue dust thickener at J&L in 1952. Joe Valles: We used to unload flue dust sometimes on the sinter plant lower track at Weirton......an old timer said it was 90% steel. A cloud eminates from it that looks like a solid wall. I made the mistake of getting too close to it, and the tiniest whiff put me on the ground. If someone was forced to breathe it, I'm sure they would die pretty quick. Really unhealthy stuff...... |
 |
Gabi Buhus commented on Bob's post Aliquippa, taken from here: [Also the stack with J&L on it is another signature of Aliquippa.] |
 |
Bob Ciminel posted J&L Steel first all-river shipment to Minneapolis. I believe this is from the Aliquippa Works, not Pittsburgh. No date given. Pat McCon: Since we made wire and pipe in Aliquippa only, that makes sense. |
 |
Bob Ciminel posted Seamless pipe mill at J&L Steel, date unknown. Edward Talmadge: Sam Burkett alot of steel that we made at J&L Pittsburgh works was for the pipe industry around 1980 and we shipped the billets to Aliquippa. James Caraway: I ran # 3 Seamless at USS, 12 3/4” through 26”- largest OD Seamless in USA. |
 |
Bob Ciminel posted Another view of the J&L Steel seamless tube mill, Aliquippa, PA Nathan Burcl: I recognize a few of these machines. Two reelers, a high mill. Two reheat furnaces. The outlet trough covers aren’t absolutely necessary and sometimes get in the way. I wonder if they got removed years later. |
 |
1 of 28 photos shared by Michael Gilmer Peter A Mamula: Great pics! Thx! At one times Aliquippa J&L was the largest steel mill in the world! |
 |
Little Beaver Historical Society posted
Cincinnati Roll Grinder J&L Steel Tin Mill Aliquippa PA. Most likely mid 1930's John Domansky Sr.: Cincy made many steel mill machines. Richard Peoples: I ran that in the summer of 1976, grinding tandem and temper mill backup rolls. Tony Dutton: Guess housekeeping wasn't a thing then huh? |
 |
David Holoweiko posted 1938 A view of the J&L (Jones & Laughlin) Coal Incline in Aliquippa, Pa. taken from aboard the Excursion Queen Saint Paul steamer David Finch: Believe there were two such installations. One for the south mill coal fired power house, near A&A bridge. Other north mills, across from Baden McDonalds that supplied the coke ovens. |
 |
David Holoweiko posted The seamless hot mills (No. 1 pictured here) produced high strength pipe that was used to drill oil wells, to case wells, and to transport oil and gas at the J&L Aliquippa Works . |
 |
David Holoweiko posted J&L Aliquippa PA Beaver County 1960. Stripper Yard and Morgan Crane.
John Horn: Great ingots picture Real Bubba: Good shot of hot tops, I worked at Bognar’s hot top plant in New Galilee. |
 |
David Holoweiko posted Number 1 scrap buggy BOF at J&L Aliquippa works .
Samuel Peoples: You should note that the picture is of the OLD No. 1 BOF. It was shut down in 1968 as too small. The N. 2 BOF Shop was up and running in 1968 producing heats that were several times the size of these heats, on the order of 200-275 tons per heat. No. 1 BOF was at best an experiment |
 |
David Holoweiko posted J&L Steel Aliquippa #1 & #2 Tin Lines 1944
Evert Kunenborg: A lot of space between the lines π€ |